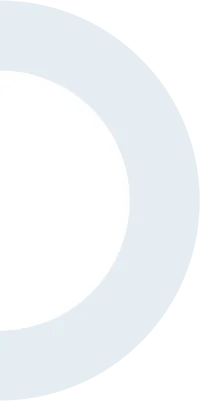
infrastructure
Managing machines and team members with utmost care.
Biloree’s production unit has been set up at Lodhika GIDC which is about 16km away from Rajkot. It spreads over 3 acres with a production capacity of 2,00,000 units per month. It is made sure that the location is kept very hygienic and the gardens are maintained thoroughly. Along with having high-tech machines and cutting-edge amenities, we also hold a sufficient loading and unloading capacity unit. Especially for centrifugal die-casting, the foundry has three heavy-duty induction furnaces. Every process carried out is fully automated and up-to-date.
In addition, we have placed an order for a Carousel Machine, which will aid the fleet’s manufacturing. All the products are manufactured with utmost care. Also, a canteen has been set up to serve complimentary meals to all of our employees. We also have geared up on our plans to increase the current manufacturing capacity.
Glimpses of our Facility
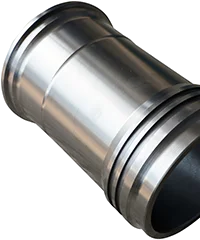
Quality Certification
Our Production Process
A transparent, accelerated and advanced way of production.
Guarantee Statement
All important manufacturing procedures, from material composition to final inspection before dispatch, are documented and evaluated to guarantee that we continuously deliver high-quality products that satisfy international standards. For instance, we use use ultrasonic cleaning for the cylinder liners for them to give best results and control value. New product design and development are also routed through APAQ Process Quality and integrated into the production process via:
Process monitoring and Operating instructions
Efficient Set-up approval
Brief Control plans and checklists
Process capability evaluation
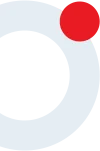